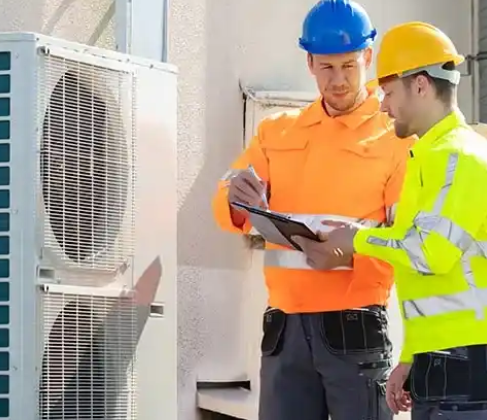
Effective supply chain management is crucial for any business, whether big or small. However, even large companies with dedicated teams can make costly mistakes. For smaller businesses, juggling various responsibilities often leads to overlooking key aspects of supply chain management. Here are eight common errors businesses make in their supply chain operations and how you can avoid them.
1. Streamlining Processes Inefficiently
A lack of efficiency in supply chain processes is a major pitfall, especially for smaller businesses. Common mistakes include relying on outdated, paper-based workflows or implementing technology before optimizing processes. To avoid this, focus on improving processes continuously, integrating technology only where it adds value. Switch to business software solutions to eliminate paper-based systems, which can significantly increase efficiency and reduce errors.
2. Overcomplicating Visibility
In the age of big data, many companies get overwhelmed by trying to monitor every aspect of their supply chain in real-time. However, it’s not necessary to track every single detail. Instead, identify key points where visibility adds the most value—order and delivery, for example. Customers expect real-time tracking, and providing them with updates not only boosts their satisfaction but also helps you prevent costly mistakes.
3. Confusing Single Sourcing with Strategy
While single sourcing may seem like an efficient strategy, it can lead to significant risks if a company becomes too reliant on one supplier. Recent disruptions have highlighted the importance of having backup suppliers. Consider diversifying your supply chain by adding secondary suppliers, even if they only meet a small portion of your demands. This can prevent disruptions if your primary supplier faces challenges.
4. Mismanaging Inventory
Inventory management is one of the most challenging and impactful areas in supply chain management. Overstocks can tie up cash, while understocking can result in lost sales and poor customer service. Balancing inventory requires the right tools. Investing in inventory management systems, such as barcode tracking or RFID, allows you to monitor inventory in real-time, reducing the risk of overstocking or understocking.
5. Neglecting Supplier Relationships
Supplier management is often overlooked but is vital for a smooth-running supply chain. Common errors include underestimating supplier risk, failing to properly vet new suppliers, or ignoring the importance of building long-term relationships. Instead, focus on strengthening partnerships with key suppliers. Maintaining open communication, setting performance metrics, and regularly reviewing supplier performance can help prevent costly disruptions.
6. Treating All Customers the Same
A one-size-fits-all approach to service delivery might work for certain products, but it’s not effective for customer service. Businesses often make the mistake of offering the same service levels to every customer, which can lead to inefficiencies and even losses. Tailoring your service levels to different customer segments ensures that resources are allocated where they are needed most and prevents net losses on sales.
7. Failing to Learn from Industry Best Practices
Many businesses make the mistake of not keeping up with best practices in supply chain management. This can result in outdated processes that don’t reflect the latest innovations. Regularly reviewing industry standards and learning from other successful companies is essential to staying competitive and avoiding operational inefficiencies.
8. Ignoring Technology’s Role in Risk Management
Risk management is crucial in supply chain operations. Ignoring the role of technology in identifying and mitigating risks can leave a business vulnerable. Implement tools like predictive analytics to identify potential disruptions and plan accordingly. By forecasting risks, you can adjust strategies proactively and minimize the impact on your operations.
Conclusion
Supply chain management is a complex but essential aspect of any business. By avoiding these common mistakes—such as inefficiencies in processes, poor visibility, single-sourcing strategies, and mismanaging inventory—businesses can create more efficient, cost-effective, and resilient supply chains. Focusing on continuous improvement in these areas will not only streamline operations but also help businesses stay competitive in an increasingly fast-paced market.