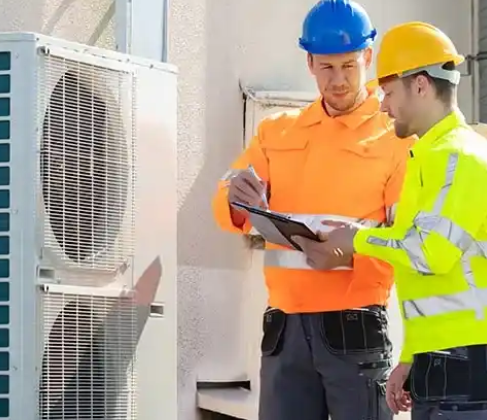
In the rapidly evolving world of industrial automation, mobile robotics has become a cornerstone of modern logistics and manufacturing systems. However, there’s still some confusion around two key players in this space: Automated Guided Vehicles (AGVs) and Autonomous Mobile Robots (AMRs). Though they may appear similar at first glance, the way these machines operate—and the environments they thrive in—are quite different.
What Sets AGVs and AMRs Apart?
At the most basic level, AGVs follow fixed paths. Their movement depends on predefined routes marked by magnetic strips, wires, or beacons. They are programmed to travel along these routes and cannot independently alter their course. If something blocks their path, they simply stop and wait for it to clear.
AMRs, on the other hand, are far more adaptive. Using sensors, cameras, and advanced software, AMRs navigate freely through spaces. They interpret their surroundings in real time, allowing them to make decisions such as rerouting when encountering an obstacle. This gives them a significant edge in dynamic and unpredictable environments.
Navigational Capabilities and Intelligence
The defining difference between the two lies in autonomy. AMRs possess onboard intelligence that enables them to operate without direct human input or external guidance systems. They process environmental data continuously, using laser scanners, depth sensors, and AI-driven algorithms to plan their routes.
AGVs lack this level of adaptability. Although some newer AGVs can detect obstacles, they still rely on static instructions and do not have the ability to reroute or interpret complex surroundings. This limits their use to highly structured spaces where tasks and paths remain consistent.
Application in Industrial Environments
AGVs are best suited for repetitive tasks in stable conditions. They’re commonly used to transport raw materials, handle packaging, or move goods from one fixed point to another. Their reliability makes them a good fit for operations with consistent workflows and minimal need for flexibility.
AMRs shine in environments that are constantly changing or shared with human workers. Their ability to adjust to shifting layouts or unexpected obstacles makes them ideal for collaborative tasks, real-time inventory transport, inspection, and even quality control processes.
Flexibility and Scalability
One of the standout features of AMRs is their adaptability. Businesses don’t need to modify their infrastructure to accommodate them. This makes AMRs highly scalable, as companies can deploy more units or expand to new areas without major layout changes.
AGVs, by contrast, require dedicated pathways and infrastructure setup before operation. Expanding or altering their work zone often involves additional costs and downtime.
Choosing the Right Solution
When deciding between AGVs and AMRs, the choice ultimately depends on the specific operational needs. If a business requires straightforward, high-volume material handling in a controlled space, AGVs may be sufficient. But for tasks that involve interaction with dynamic environments or require more advanced decision-making, AMRs are the better fit.
In sectors like logistics, manufacturing, agriculture, and construction, AMRs are being increasingly adopted due to their versatility and intelligent behavior. Their ability to perform complex tasks without constant supervision aligns perfectly with the goals of modern Industry 4.0 initiatives.
As factories and warehouses continue to evolve, understanding the distinct roles of AGVs and AMRs becomes essential. While both have their place in automation, the future points toward smarter, more autonomous systems that can seamlessly adapt to the needs of intelligent industrial operations.