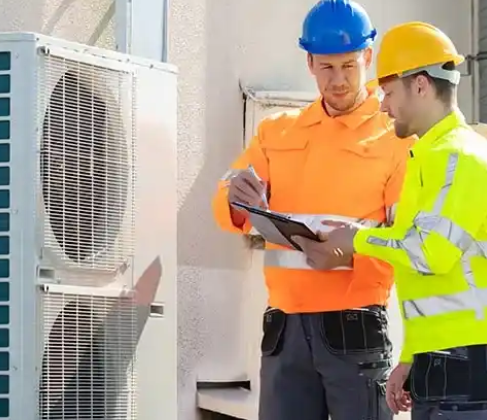
As automation reshapes the manufacturing world, two key types of robotic systems continue to gain attention: industrial robots and collaborative robots. While both are products of the broader evolution in robotics driven by Industry 4.0, they serve different purposes and are designed to operate under distinct conditions. Recognizing the differences between them is essential for choosing the right solution for each specific production need.
Industrial Robots: Power, Speed, and Specialization
Industrial robots were among the first forms of automation introduced on production lines. Built for heavy-duty tasks, these machines are typically large, stationary units designed to operate at high speeds and with extreme precision. Their role is to execute a single task continuously, such as welding, assembly, or material handling, often in environments where human presence is limited due to safety constraints.
These systems usually require customized setups, including protective barriers or fencing, and are installed in fixed locations within a facility. Because of their complexity and capacity, they are often programmed and maintained by specialized engineers. Their efficiency and reliability make them indispensable for mass production environments such as automotive and food processing industries.
However, this level of automation requires significant infrastructure. Many traditional systems like AGVs (Automated Guided Vehicles), which were early mobile robotic solutions, depended on physical guides such as beacons or magnetic strips and lacked the flexibility to adapt to dynamic environments or handle unexpected obstacles.
Collaborative Robots: Flexibility and Human Interaction
Collaborative robots, often referred to as cobots, were developed with a different purpose in mind. Rather than replacing human labor, these systems are designed to work alongside it. Lightweight, compact, and mobile, cobots are intended for easy integration into existing workflows. Their adaptability allows them to assist in various tasks without the need for significant layout changes or safety barriers.
A defining characteristic of collaborative robots is their built-in safety features. Equipped with sensors that detect proximity or motion, they can automatically slow down or stop when a person enters their workspace. This ensures safe cooperation between robots and humans on the factory floor.
Cobots are designed to handle multiple tasks—from part assembly and inspection to packaging and surface finishing. Their flexibility and ease of use allow operators with minimal technical training to reprogram them for different functions, which is especially beneficial in settings that require frequent adjustments to production lines.
Collaborative Mobile Robots (CMRs): A Step Further in Autonomy
CMRs combine the benefits of collaborative robotics with mobility, giving them the ability to move autonomously throughout a facility. Unlike traditional AGVs, CMRs don’t rely on fixed infrastructure and can adapt to new routes or tasks quickly. These robots are used for transporting materials, assisting with repetitive manual processes, or handling tasks that require both movement and manipulation.
Mobile manipulators, a category within CMRs, integrate robotic arms onto mobile platforms. They are highly effective for operations like pick-and-place, feeding machines, polishing, drilling, or cleaning. Their mobility dramatically increases the robot’s usable workspace, making them suitable for diverse industrial environments.
Comparing the Two: Purpose and Application
The primary distinction between industrial robots and collaborative robots lies in their intended use:
- Industrial Robots are built for maximum speed, accuracy, and durability. They specialize in a single, repetitive task, and their operation is best suited for structured environments with minimal human interaction. They are ideal for companies focused on high-volume, consistent output.
- Collaborative Robots are designed for versatility and direct interaction with human operators. Their strength lies in their ability to adapt to various tasks, integrate quickly, and improve workflow without requiring extensive changes to the production layout.
Where industrial robots are often seen as replacements for human labor, cobots function as partners—sharing workloads, enhancing safety, and increasing efficiency across departments.
Both types of robots offer significant benefits, and their roles are not in competition but rather complementary. As factories continue to evolve, many will adopt a hybrid approach—leveraging the power of industrial robots where precision and speed are paramount, and relying on collaborative systems where flexibility and human interaction are essential. This balance is what defines the future of smart manufacturing.