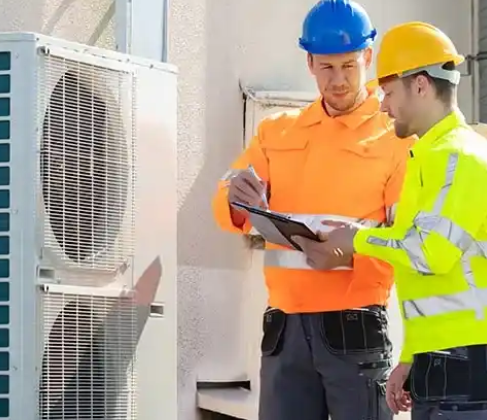
B2C logistics refers to the process of delivering products directly from businesses to consumers. As e-commerce continues to grow, so does the complexity of B2C logistics, especially with rising expectations for faster delivery and more flexible fulfillment.
Key Elements of B2C Logistics
1. Warehouse Management
Effective warehouse management is essential for B2C logistics. It involves organizing inventory, maintaining stock levels, and ensuring items are ready for quick picking and packing. Modern warehouses often leverage automation and robotics to streamline operations, allowing businesses to efficiently handle the high volume of consumer orders.
2. Order Processing
Once a customer places an order online, a series of events are triggered, from inventory checks to packaging and shipping label generation. Warehouse Management Systems (WMS) help automate and coordinate these processes, ensuring orders are processed swiftly and accurately.
3. Last-Mile Delivery
The last mile is the final and often most expensive leg of B2C logistics, involving the delivery of packages from distribution centers to customers’ doorsteps. This stage comes with its own set of challenges, including dealing with delivery failures, signature requirements, and varying customer preferences for delivery time and method.
B2C vs B2B Logistics
One of the primary differences between B2C and B2B logistics is the type of orders being handled. B2B logistics typically deals with large quantities of products shipped to businesses or stores, while B2C logistics involves numerous small orders being sent directly to individual consumers. These differences require distinct equipment, processes, and technology. For example, B2C warehouses need more packing stations and a more advanced returns process, as consumer return rates can range from 20-30%.
Here’s a comparison of B2B and B2C logistics:
Aspect | B2B Logistics | B2C Logistics |
---|---|---|
Order Volume | 50-200 orders | 1000+ orders |
Order Size | Large quantities per order | Mostly single items |
Storage Systems | Pallet racking, bulk storage | Dense picking areas, automated systems |
Technology Needs | Basic WMS, inventory tracking | Advanced OMS, real-time inventory |
Delivery Timeframes | Scheduled 2-3 days | Same/next-day delivery, real-time tracking |
Returns Rate | 5% average, full pallets | 20-30% in fashion, 10-15% general merchandise |
Peak Handling | Quarterly peaks, predictable volumes | 10x volume spikes, weekend peaks |
Quality Control | Batch sampling | Individual order checks |
Labor Requirements | Stable workforce | Flexible staffing, dedicated returns team |
Challenges in B2C Logistics
The digital transformation has made B2C logistics more dependent on real-time tracking and automated communication systems. Companies need the ability to track inventory, provide delivery status updates, and communicate efficiently with customers.
One of the biggest challenges in B2C logistics is managing delivery costs while meeting consumer expectations for fast, free shipping. Additionally, the rising volume of returns poses a significant issue, especially with industries like fashion seeing return rates as high as 20-30%. To address these challenges, many companies are turning to micro-fulfillment centers located closer to urban areas and collaborating with local delivery services to reduce delivery times and costs.
Meeting the Demands of Modern B2C Logistics
To succeed in B2C logistics, businesses must adapt to the fast-changing landscape of consumer expectations. This involves investing in digital infrastructure for real-time tracking, flexible operations to handle peak periods, and innovative solutions for reducing the costs associated with delivery and returns. Companies that can master these elements will be better positioned to thrive in the competitive world of e-commerce.