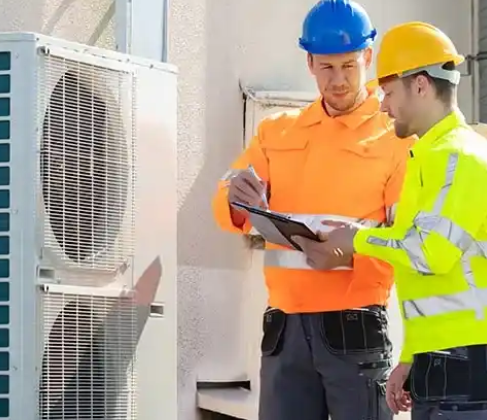
Cross docking is a concept that sounds simple in theory but is often challenging to execute effectively. Without stored inventory to buffer against disruptions, operators must rely on precise synchronization between inbound and outbound shipments. If any part of the process falters, it can lead to delays and extra costs, which can impact customer satisfaction and operational efficiency.
To keep your cross-docking operations running smoothly and effectively, here are six strategies to boost efficiency and streamline the process.
1. Optimize Material Flow Systems
Gone are the days of relying solely on gravity conveyors. To achieve high efficiency, modern cross-docks use a blend of proven and emerging technologies. Some key solutions include:
- Modular conveyor networks that adapt to varying volumes
- Zone-specific automation to tackle bottlenecks in high-traffic areas
- Mobile robots (AMRs) for flexible pallet handling during peak periods
- Smart sorters with scan-and-go features for faster package routing
When selecting technology, it’s essential to tailor the mix to your operation. For smaller facilities handling 50-75 trailers daily, basic conveyors and a few AMRs might suffice. For larger operations with 200+ trailers, consider full automation in your staging areas. A good ROI can be achieved within 18-24 months when automation is scaled properly, with the highest-volume lanes being prioritized first.
2. Keep the Dock Area Clean and Organized
A cluttered dock can hinder efficiency, especially when forklifts and other equipment are blocked by obstacles. Ensuring the dock area is clean and organized is crucial not just for safety but for optimizing operational flow. A tidy workspace promotes smoother handling and quicker transitions, leading to greater productivity.
3. Maximize Space Efficiency
While it may seem tempting to use a large space for your cross-dock, more space can actually increase travel time between inbound and outbound trucks. By using a more compact layout, you can reduce travel distances and improve efficiency. This is especially true if your facility is well-maintained and organized according to tip #2.
4. Ensure Ample Yard Space
Since cross docking involves staging trailers for both inbound and outbound shipments, it’s essential to have enough yard space to accommodate the trailers in queue. Sufficient yard space helps prevent bottlenecks, making it easier to manage the flow of goods and maintain an efficient operation.
5. Implement a Dynamic Staging Strategy
The traditional fixed-door assignment system often leads to inefficiencies and delays. Instead, modern cross-docks should use dynamic staging based on real-time conditions. Effective strategies include:
- Integration with yard management systems (YMS) to track trailer locations and dwell times
- Use of door scoring algorithms that account for carrier reliability and shipment volume
- Digital dock scheduling that provides 15-minute appointment windows to avoid congestion
- Load profile analysis to adjust door assignments weekly based on patterns
These systems allow for better allocation of resources, reducing travel distances and improving productivity. For example, a cross-dock in Chicago handling retail distribution reduced trailer dwell time from 95 minutes to 67 minutes simply by adjusting their door assignments and scheduling.
Key metrics to track include:
- Door utilization rate (aim for 85%+)
- Dock-to-dock time per pallet
- Travel distance per movement
- Trailer queuing time in the yard
6. Embrace Advanced Technology
Integrating technology into your cross-docking operation is essential for maximizing efficiency. Some of the most effective tech solutions include:
- Core systems integration: Use cloud-based WMS/TMS systems that connect directly with your carriers for accurate ETAs and scheduling.
- Mobile apps: Enable drivers to check in and receive door assignments directly from their phones, streamlining the process and reducing wait times.
- Task management apps: Help workers prioritize tasks, track productivity, and follow digital checklists for quality control.
- Performance tracking: Use live dashboards to monitor throughput, carrier compliance, and dwell times in real time.
The key to success here is ensuring that your team adopts and utilizes these tools effectively. Start by focusing on core systems like scheduling and real-time visibility before integrating more complex features such as predictive analytics.
The Role of a Strong Team
While cross docks don’t require a traditional picking operation, they are still bustling workplaces that require precise coordination. Efficient unloading, staging, sorting, and vehicle coordination are all critical tasks that must be carried out seamlessly. The success of a cross-docking operation depends on having a skilled team in place to supervise these processes. Selecting the right personnel for key roles is crucial, as synchronization is key to maintaining an efficient flow of goods.
By implementing these six tips and focusing on having the right team, you can optimize your cross-dock operations, reduce costs, and ensure faster deliveries, all of which will benefit your supply chain efficiency.