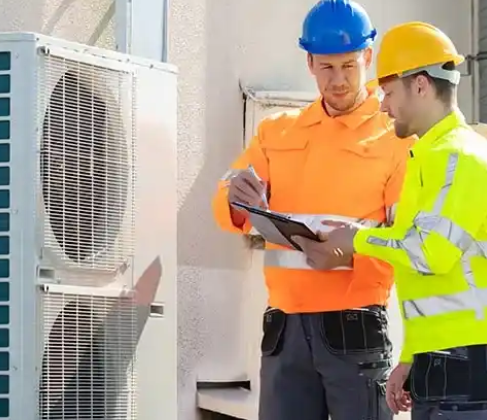
The gig economy has been on the rise, with more professionals opting for freelance work over traditional employment. Data science has become one of the most popular freelance sectors, with professionals leveraging their expertise in data analysis and machine learning to provide valuable insights for businesses worldwide. The increasing demand for remote work has only boosted this trend, making it easier for companies to hire freelance data scientists for specialized tasks.
If you’re considering transitioning into freelance data science, whether you’re just starting out or looking to take the plunge into the gig economy, it’s important to understand both the opportunities and challenges that come with it. This blog post will guide you through the benefits and drawbacks of freelance data science, provide tips for getting started, and share advice on how to succeed as a freelancer in this rapidly growing field.
Benefits of Freelance Data Science
Freelancing in data science offers many advantages for professionals looking for autonomy and flexibility. If you’re self-driven, skilled at managing client relationships, and have a good track record in data science, freelancing could be the ideal choice for you.
One of the main perks is the flexibility to choose projects that align with your interests and values. As a freelance data scientist, you have the freedom to work on a variety of data projects, which allows you to build a diverse portfolio. Plus, freelancing eliminates the need for a daily commute and provides the freedom to set your own schedule, a major advantage for those looking to improve work-life balance.
For those new to freelancing, it might take some time to establish yourself, but once you’ve built a reputation for quality work, you’ll be able to negotiate higher rates and work on more complex projects. As you grow your freelance career, you’ll gain valuable experience in managing both the technical and business aspects of data science, which can help elevate your career to new heights.
Drawbacks of Freelance Data Science
While freelancing offers independence and flexibility, it also comes with its fair share of challenges. As a freelance data scientist, you’ll need to handle much more than just technical tasks. You’ll also need to market your services, manage client relationships, and ensure a steady stream of work, which can add pressure.
Some common challenges of freelance data science include:
- Unstable income: Unlike a salaried job, freelancers are paid per project. This means that you must continually find new clients, market your services, and build a steady client base.
- Administrative tasks: Freelancers handle their own business aspects, such as negotiating contracts, setting rates, and understanding self-employment taxes, all of which can be time-consuming.
- Lack of employee benefits: Freelancers don’t have access to health insurance, retirement plans, or paid time off, so you’ll need to arrange these benefits independently.
- Isolation: Working independently means you might miss out on team collaboration, which can lead to feelings of isolation and stress. Without regular team interactions, staying motivated and productive can become more challenging.
Despite these challenges, many data scientists thrive in the freelance world by being organized and managing their time effectively. If you’re ready to take on these responsibilities, freelancing can be a rewarding path.
How to Become a Freelance Data Scientist
Starting as a freelance data scientist requires more than just technical skills—it also involves building your brand, finding clients, and managing multiple projects. Here are a few key steps to get started:
Networking and Building Your Presence
Building a solid presence as a freelancer takes time, but it’s an investment that will pay off. The first step is to identify your niche and focus on areas of data science that match your expertise. Consider publishing articles, tutorials, or case studies on platforms like Medium, or sharing insights on LinkedIn to increase your visibility.
Here are some ways to build your network:
- Engage with industry groups and attend events (even virtually) to meet potential clients.
- Create a profile on freelance platforms like Fiverr, Upwork, or Freelancer to showcase your expertise.
- Share your knowledge and participate in discussions on data science forums or social media platforms.
Finding Opportunities
As a freelancer, it’s crucial to actively seek out new opportunities rather than waiting for them to come to you. Don’t hesitate to reach out to companies or organizations that interest you, even if they aren’t currently advertising freelance roles. Networking with employees in companies you’re interested in can sometimes reveal hidden job opportunities that aren’t posted publicly.
Always encourage your previous clients to write testimonials or provide referrals. The more positive feedback you receive, the easier it will be to attract future clients.
Crafting Winning Proposals
When you find a potential project, it’s essential to create a compelling proposal. Tailor your proposal to the specific needs of the client, highlighting your experience and how you can address their unique challenges. A well-crafted proposal can make the difference between winning or losing a project.
A good proposal includes:
- An engaging overview that shows the value you bring to the client
- A clear problem statement and your proposed solution
- A transparent pricing structure
- A timeline that aligns with the client’s expectations
- A call to action to encourage the client to contact you
Managing Multiple Projects
As a freelancer, you’ll likely juggle multiple projects at once. Time management becomes crucial to avoid burnout. Here are some tips to help you stay organized and efficient:
- Automate billing: Use tools that help manage your finances and payments so you can focus more on your projects.
- Set clear pricing: Research fair rates for data science work to ensure you’re paid appropriately for your time and expertise.
- Maintain work-life balance: Be sure to set boundaries and avoid overcommitting. Unplug from work during off hours and make time for rest and relaxation.
Conclusion
Freelance data science can be a highly rewarding career choice if you are prepared for the autonomy and challenges it entails. With the right mindset and a proactive approach, you can build a thriving freelance career in the growing field of data science. By continuously improving your skills, networking, and managing client relationships, you’ll find yourself well-positioned for success in the competitive gig economy.
Comments