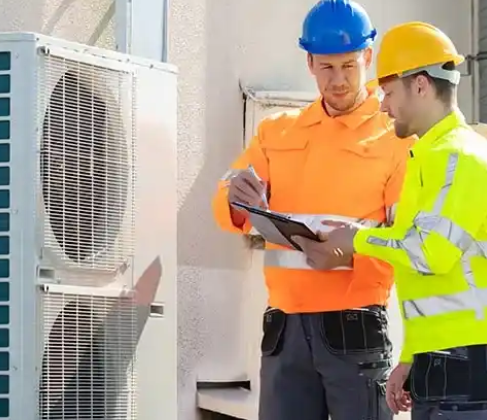
As a business owner, the moment a potential customer lands on your website, they form an opinion in less than three seconds. This rapid judgment will determine whether they stay and engage or bounce away, potentially losing you valuable revenue. According to studies by Nielsen Norman Group, people make up their mind about your website in just 50 milliseconds – that’s a mere 0.05 seconds.
For many businesses, this harsh reality translates into high bounce rates. A bounce rate between 40-60% is common, with some industries seeing numbers soar as high as 80%. Each bounce represents a missed opportunity, and even slight improvements can lead to significant revenue increases. A study by a Fortune 500 company revealed that a 1% improvement in their bounce rate led to an additional $2 million in annual revenue.
So, what’s causing these bounces? Over the past year, I’ve analyzed hundreds of business websites, and certain patterns have become clear. There are specific design and technical issues that consistently drive visitors away before they can even interact with your brand.
Here are the key warning signs that your website may be turning potential customers into lost opportunities.
1. Slow Website Loading Speeds
There’s nothing more frustrating than waiting for a website to load. If your website feels like it’s stuck in the dial-up era, you’re likely losing visitors right away. A Google study found that the chance of visitors bouncing increases by 32% when page load time goes from one to three seconds. After five seconds, that rate jumps to 90%.
This is more than just an inconvenience. For every additional second of load time, conversions drop by approximately 7%. Retail giant ASOS found that for every extra second their site took to load, conversion rates fell by 10%. After improving their load speed, they saw a 5% increase in conversions and $600,000 in extra sales.
Moreover, site speed impacts search engine rankings. Google uses loading speed as a ranking factor, so slow sites are buried lower in search results, further compounding the issue. Thankfully, many speed-related issues can be fixed with simple changes like compressing images or using content delivery networks.
2. Mobile Experience Is Poorly Optimized
Mobile traffic now accounts for more than 60% of all internet traffic, yet over half of websites still provide poor mobile experiences. Research shows that 88% of users won’t return to a site after a bad mobile experience. Even worse, 52% of customers are less likely to engage with a company after a poor mobile encounter.
Some common mobile issues include text that’s too small to read, buttons that are too close together, and forms that are hard to complete on small screens. These problems increase the likelihood of abandonment.
For example, we worked with an e-commerce client whose mobile site took 11 seconds to load. After implementing mobile-specific optimizations, their conversion rate improved by 137%, leading to an additional $382,000 in revenue.
Mobile optimization isn’t just about making your site fit on a phone – it’s about tailoring the experience for mobile users. This means touch-friendly navigation, easy-to-read text, and forms that are optimized for thumb use.
3. Confusing Website Navigation
Your website’s navigation should be simple and intuitive, like a well-organized highway system. Unfortunately, many businesses make navigation so complicated that visitors struggle to find what they need. Research from Baymard Institute reveals that 37% of users leave a website if they can’t easily find what they’re looking for in the navigation.
The consequences are serious. Websites with complex navigation structures see conversion rates up to 219% lower than those with clear, simple navigation.
For example, we helped a B2B software company whose visitors were spending just 49 seconds on their site. After analyzing their heatmaps, we realized their visitors were playing “navigation roulette,” clicking randomly through confusing menus. After restructuring the navigation, average session duration increased to 3 minutes and 12 seconds, leading to a 34% improvement in lead generation.
The solution? Think about your customers’ needs when organizing your website, not how your internal team organizes information.
4. Content Isn’t Structured for Scanning
Eye-tracking studies show that visitors don’t read every word on a webpage. Instead, they scan in an F-shaped pattern. If your content doesn’t align with this natural reading behavior, visitors will likely miss important information, leading to frustration and bounces.
For instance, one of our retail clients had a high cart abandonment rate because key selling points (like free shipping and hassle-free returns) were buried at the bottom of product pages, outside the F-pattern zone. By restructuring the content to highlight these points where users naturally look, cart abandonment dropped by 15% and generated an estimated $417,000 in additional annual revenue.
Effective content organization involves using clear headlines, concise paragraphs, strategic subheadings, and visual elements that guide the reader’s eye.
5. Lack of Trust Signals
Building trust is essential for any website. If your site looks unprofessional or lacks trust signals like security badges or contact information, visitors may feel uneasy and leave. Research shows that 93% of consumers consider trust to be a crucial factor in deciding where to shop online.
Common trust issues include outdated design, missing contact information, and lack of security certifications. One healthcare client had a 78% bounce rate on their booking page due to missing trust signals, like HIPAA compliance and practitioner credentials. After adding these elements, their conversion rate improved by 62%, generating $287,000 in additional revenue.
Building trust involves more than avoiding negative signals – it requires proactively demonstrating credibility through design, transparency, and security.
6. Ineffective Calls-to-Action
A website without clear calls-to-action (CTAs) is like a store without checkout counters. Visitors may browse but won’t take any measurable action. Surprisingly, 43% of small businesses lack clear CTAs on their landing pages, which leads to missed opportunities.
Ineffective CTAs lead to what conversion experts call “dead-end pages,” where visitors consume content but don’t take any action. We saw this with a professional services client whose redesigned website was underperforming. Their primary service pages ended with vague “Contact Us” links. After replacing them with value-driven CTAs like “Get Your Free Consultation,” lead generation increased by 43%.
Effective CTAs should be clear, action-oriented, and placed strategically on the page to capture visitors’ attention.
7. Lack of Proper Analytics Tracking
Many business owners operate without a clear understanding of their website’s performance. While most websites use Google Analytics, fewer than a quarter have it properly configured to track meaningful conversion actions. Without proper analytics, it’s impossible to identify what’s driving visitors away.
For example, we helped a manufacturing client who wasn’t seeing any leads from their redesigned website. After auditing their analytics, we discovered they weren’t tracking form submissions. By simplifying a complex form field, they increased lead submissions by 57%, resulting in $680,000 in additional revenue.
Proper analytics tracking isn’t just about collecting data; it’s about using it to identify friction points and opportunities for improvement.
Diagnosing High Bounce Rates
To diagnose a high bounce rate, check your Google Analytics for bounce rates above 70%. Next, test your site on mobile devices and ensure it’s optimized. Evaluate your website’s speed using tools like Google PageSpeed Insights, and check your navigation for usability issues. Finally, ensure your site has trust signals and clear CTAs.
Moving from Bounce to Conversion
The good news is that most of these issues can be fixed with the right strategies. Improving website performance typically leads to exceptional ROI, as evidenced by a client whose bounce rate dropped by 36%, leading to a 32% increase in revenue.
The path from high bounce rates to conversions starts with a comprehensive website analysis. With the right changes, your business can maximize the value of each visitor, improving both engagement and revenue.
Comments