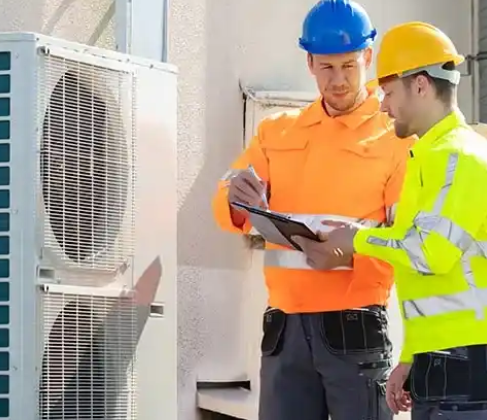
The integration of autonomous mobile robots into industrial operations has reshaped how production and logistics tasks are performed. These robots are not just improving processes—they’re redefining the role of human labor by taking over tasks that are often undesirable or unsafe. At the heart of their utility lies the concept of the “4 D’s”: Dull, Dirty, Dangerous, and Dear. These categories represent the tasks best suited for automation due to their monotony, risk, or cost.
Let’s take a closer look at how industrial robots are transforming operations by addressing each of the 4 D’s.
Replacing the Dull: Robots for Repetitive Work
Repetitive, mundane tasks have long been a source of worker fatigue and low productivity. Activities that require little cognitive effort but significant time—like scanning items, sorting packages, or moving goods from one end of a warehouse to another—are ideal candidates for automation.
Autonomous mobile robots (AMRs) now handle these jobs with speed and consistency. In logistics centers, for example, AMRs take over the daily grind of internal transport, allowing human workers to focus on decision-making and oversight roles. This shift not only boosts morale but also raises overall output by allowing people to contribute where creativity and problem-solving are needed.
Agriculture is also benefiting from automation. Robots like those used in planting or harvesting can complete repetitive tasks more efficiently and without fatigue, helping farmers maximize output while reducing manual labor.
Handling the Dirty: Automation in Harsh Environments
Some workplaces are inherently unclean or hazardous. Industries such as mining, chemical processing, or waste management expose workers to toxic materials or unsanitary conditions. In these settings, deploying robots not only improves efficiency but also safeguards employee health.
For instance, robots are increasingly used in environments involving hazardous waste, such as electronic recycling plants. These machines can handle tasks involving toxic chemicals or harmful debris, minimizing the risk to human operators. Robots are also used for tunnel inspections or in disaster-stricken zones, where unstable ground and unknown risks make human presence unsafe.
Mitigating the Dangerous: Reducing Risk with Robotics
Safety remains a top priority across industries, particularly in sectors like construction or heavy manufacturing. Robotics provides a practical solution for minimizing exposure to dangerous situations.
Autonomous robots are now tasked with surveying deteriorating structures, performing building demolitions, or navigating unstable environments. Their ability to operate in hazardous areas eliminates the need to place humans at risk, while also offering reliable data collection and reporting.
In infrastructure and industrial inspections, robots can enter tight or risky spaces, identifying potential hazards before they cause harm. This proactive use of robotics is shifting the safety paradigm and helping companies avoid costly incidents.
Addressing the Dear: Cutting Operational Costs
High operational expenses—whether from labor shortages, inefficient processes, or material waste—are a common challenge in manufacturing and logistics. Mobile robots address this issue by delivering consistent, high-speed performance with minimal downtime.
These robots are highly adaptable, capable of switching between tasks without the need for reconfiguration. In warehouses, they optimize travel routes and reduce transport times, lowering energy use and wear on equipment. They also minimize product damage through careful handling, helping reduce waste and rework.
Robots can operate continuously, requiring only minimal maintenance or charging periods, which translates into higher output and fewer disruptions. Over time, these cost savings make robotics a sound investment for companies aiming to increase efficiency and maintain competitiveness.
Looking Forward: The Evolution of Robotics in Industry
Although mobile robotics has already made a significant impact, technological developments in artificial intelligence, machine vision, and IoT integration are pushing capabilities even further. Robots are gaining the ability to make complex decisions, work collaboratively with humans, and adapt to new tasks with little intervention.
For instance, in smart agriculture, robots are learning to distinguish between crops and weeds to reduce chemical usage. In manufacturing, connected robots can feed real-time data into analytics systems, enabling predictive maintenance and better planning.
These advancements also emphasize the value of human-robot collaboration. As robots manage the tedious or dangerous aspects of a job, human workers are empowered to focus on tasks that require insight, judgment, and adaptability.
Conclusion: Industrial Robots as Strategic Assets
By targeting the 4 D’s—tasks that are dull, dirty, dangerous, or expensive—industrial robots bring measurable improvements in productivity, safety, and cost control. They offer the ability to scale operations, ensure consistent quality, and respond quickly to market demands.
Adopting mobile robotics is no longer just a technical upgrade—it’s a strategic decision that enhances a company’s agility and global competitiveness. As technology continues to advance, the role of industrial robots will only expand, unlocking new possibilities for smarter, safer, and more efficient work environments.
Comments