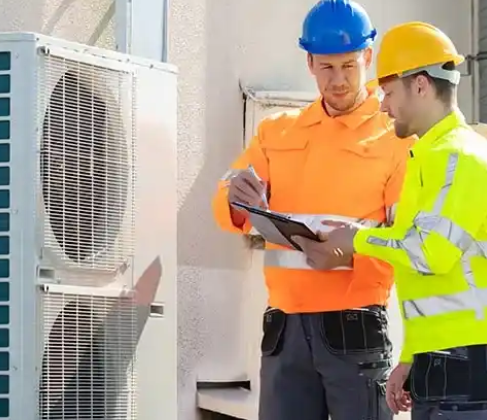
In the era of cloud computing, businesses need to be aware of data sovereignty and its critical role in data security and compliance. If you’re storing or processing data across borders, understanding the rules and regulations governing its location is vital for safeguarding both your business and customer trust. Here’s a breakdown of what data sovereignty means and how to ensure compliance with cloud storage.
What is Data Sovereignty?
Data sovereignty refers to the idea that digital data must comply with the laws of the country where it is physically stored. It’s more than just a buzzword—it’s about legal compliance, protecting your business from potential risks, and ensuring customer confidence. With numerous privacy laws across the globe, businesses must be aware of the various regional requirements and how they affect cloud storage.
Why Data Sovereignty Matters
Understanding and adhering to data sovereignty laws is essential for any business handling sensitive data. Here’s why it’s important:
- Legal Compliance: Data stored across borders must adhere to the regulations of the country it resides in.
- Customer Trust: Ensuring data protection laws are followed builds customer confidence and strengthens relationships.
- National Security: Protecting sensitive data from potential breaches is critical for both national security and corporate reputation.
Major Laws Around Data Sovereignty
Data sovereignty laws vary by region, making it essential for businesses to understand the requirements of the countries where they operate. Some key regulations include:
- GDPR (General Data Protection Regulation): This EU regulation protects the data of EU citizens, and businesses must ensure they meet the strict guidelines when processing data.
- CCPA (California Consumer Privacy Act): A privacy law in California that gives residents more control over their personal data.
- PIPL (Personal Information Protection Law): A law in China that dictates how companies handle personal data, including storage within the country.
How to Stay Compliant with Data Sovereignty
To comply with data sovereignty laws and safeguard your business, follow these key steps:
- Know Your Data: Understand the type of data you collect, store, and process, including sensitive information that may be subject to specific laws.
- Understand Local Laws: Stay updated on the data protection regulations in every country where your data is processed or stored.
- Enhance Security: Implement strong encryption and conduct regular security audits to ensure data protection.
- Choose Compliant Cloud Providers: Work with cloud storage providers who follow regional regulations and offer secure, sovereign cloud options.
- Conduct Regular Compliance Checks: Since data laws evolve, schedule regular audits to ensure ongoing compliance.
Organizing and Tracking Your Data
Before diving into security measures, it’s essential to organize and track your data to meet data sovereignty requirements:
- Categorize Your Data: Identify types of data such as customer information, financial records, or internal documents, and separate them based on their sensitivity.
- Mark Sensitive Data: Label any data governed by strict laws, like personal information under GDPR or financial data under banking regulations.
- Create a Data Map: Develop a data map that outlines where each category of data should be stored based on legal requirements. For example, EU citizen data must be stored within the EU.
Review Your Cloud Storage Setup
Once you’ve categorized your data, it’s time to assess where your data is actually stored:
- Audit Your Cloud Services: List all the cloud services you use and determine where each type of data is stored.
- Check Data Center Locations: Inquire with your cloud providers about the specific locations of their data centers.
- Compare with Your Data Map: Ensure that your data storage locations align with your data sovereignty requirements.
Setting Up Robust Security Controls
Now that you understand where your data is stored, securing it becomes the next priority. Consider these security controls to ensure your data stays protected:
- Encryption: Use end-to-end encryption for data both at rest and in transit to protect against unauthorized access.
- Zero Trust Security: Implement a Zero Trust model where each access request is thoroughly vetted, ensuring that no one is automatically trusted, even if they are inside your network.
- Role-Based Access Control (RBAC): Limit access to sensitive data based on job roles. This ensures that only authorized personnel can view or modify specific types of data.
- Multi-Factor Authentication (MFA): Add an additional layer of security by requiring multiple forms of verification before granting access to sensitive data.
Regular Monitoring and Audits
Keeping your cloud storage setup secure is an ongoing process. Regular checks are essential to stay compliant with data sovereignty laws:
- Automated Monitoring: Set up tools to monitor for unusual access patterns or unauthorized data movement.
- Compliance Audits: Regularly review your data handling processes to ensure you’re meeting legal requirements.
- Penetration Testing: Conduct regular security tests with ethical hackers to identify and fix vulnerabilities.
Working with Cloud Providers
Choosing the right cloud provider is crucial when it comes to ensuring data sovereignty. Here’s what to look for:
- Data Centers in the Right Regions: Ensure your provider has data centers in countries where your data needs to stay, or one that complies with the necessary regulations.
- Compliance Certifications: Look for providers with certifications like ISO 27001 that demonstrate their commitment to data protection.
- Sovereign Cloud Options: Some providers offer customizable options that ensure compliance with specific local laws.
The Ongoing Process of Data Sovereignty
Staying compliant with data sovereignty laws is not a one-time task—it requires continuous effort. Here’s how to stay ahead:
- Regular Internal Audits: Set up a schedule to regularly review your data handling practices.
- Stay Informed on Legal Updates: Monitor changes in laws and regulations across the regions where you operate.
- Update Policies: Ensure that your data management policies are up-to-date with the latest legal requirements.
Conclusion
Data sovereignty is a critical issue for businesses using cloud storage. By understanding the rules, choosing the right cloud providers, implementing strong security measures, and maintaining compliance through regular audits, you can safeguard your data and build trust with your customers. Data sovereignty isn’t just about avoiding penalties—it’s about taking responsibility for the data you handle and ensuring its security and privacy.
Comments