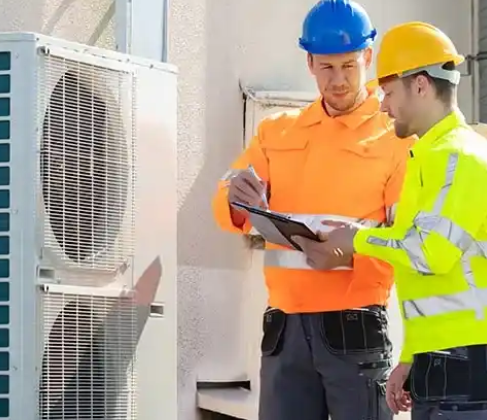
As a CEO, understanding the intricacies of your supply chain can make a significant difference in the success of your business. Even if you’re not directly managing supply chain operations, your awareness of its vital role and potential areas for improvement is essential. This article covers six crucial things every CEO should know about their supply chain to drive growth and maintain a competitive edge.
1. Has Our Supply Chain Been Strategically Developed?
A fundamental question for any CEO is whether the supply chain has been built with long-term strategy in mind. Has it evolved organically, or has it been strategically designed and regularly updated to align with business goals? Many companies fail to periodically review their supply chain, which can result in inefficiencies. For example, the location of your warehouses should be based on strategic decisions, not just legacy choices. If the supply chain has not been optimized for your current business needs, it’s time to take a closer look and make adjustments.
2. Do We Have the Right People in Key Supply Chain Roles?
A well-structured supply chain team is crucial, yet many companies place people in leadership roles without the necessary supply chain expertise. If your supply chain managers lack experience, it could be a sign that the function has not been given the priority it deserves. CEOs need to evaluate whether supply chain leadership is valued and whether the team is equipped with the right skills to manage a modern, effective supply chain. Having the right people in these roles can help drive better decision-making and ultimately improve operational performance.
3. Are Our Business and Supply Chain Strategies Aligned?
It’s essential for the supply chain to support overall business objectives. If your company is pursuing growth while focusing heavily on cost-cutting within the supply chain, it’s unlikely that both strategies will work harmoniously. Misalignment can lead to operational friction and unmet customer expectations. By aligning the supply chain strategy with business growth objectives, CEOs can ensure that the supply chain contributes to rather than detracts from company success. This doesn’t mean sacrificing cost control, but rather focusing on efficiency and value creation.
4. Are We Using the Right Metrics and Incentives?
To gauge supply chain performance, it’s critical to use the right metrics and ensure that incentives drive the right behaviors. Performance indicators should align with company-wide goals and encourage cross-functional collaboration. CEOs should ask whether the metrics in place foster a siloed approach or promote an enterprise-wide strategy. When performance measurements are fragmented, it’s often a sign that supply chain integration is lacking. It’s important to establish a measurement system that encourages teamwork and drives business-wide success, not just departmental success.
5. Have We Built Quality into Our Supply Chain?
Operational quality is a crucial aspect of supply chain management. CEOs should understand that building quality into the supply chain is not just about inspection but about creating processes that prevent defects and ensure consistency. Quality can be embedded at various stages, from standardizing processes to managing supplier performance. By focusing on continuous improvement and addressing risks proactively, companies can enhance supply chain reliability and create a competitive advantage. This is a long-term, iterative process that pays off by reducing defects and improving customer satisfaction.
6. Are We Focusing on Supply Chain Efficiency?
Efficiency in the supply chain directly impacts operating costs and the cost of goods sold (COGS). Many companies overlook opportunities to streamline operations, often because changes could affect customer service. However, CEOs should be aware that improving efficiency can lead to significant cost reductions without sacrificing service quality. For example, offering tiered service levels based on customer needs can help optimize resources and improve profitability. Additionally, improving distribution network optimization, investing in safety measures, and increasing supply chain visibility can also enhance efficiency.
Why CEOs Should Prioritize Supply Chain Knowledge
As a CEO, understanding your supply chain’s strengths and weaknesses is crucial for navigating challenges and seizing opportunities. CEOs who are involved in their supply chain operations can drive meaningful changes that lead to improved performance and competitive advantage. Instead of waiting for issues to arise, proactive involvement can help avoid costly disruptions and protect your company’s reputation.
By asking the right questions and working closely with supply chain leaders, CEOs can foster a culture of collaboration and continuous improvement that will benefit the entire organization. Understanding the supply chain is not just a matter of operational efficiency—it’s a key driver of long-term business success.
Comments