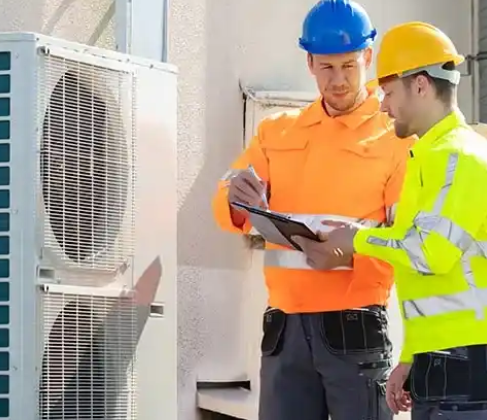
In the fast-paced world of supply chain and logistics, mobile robotics is emerging as a pivotal force in driving transformation. As companies seek smarter and more responsive systems to meet growing demands, autonomous mobile robots are becoming key tools in reshaping operations, improving productivity, and enhancing flexibility across the entire logistics network.
This article explores how mobile robots are redefining warehouse operations, their integration into existing systems, various robot types available, and the essential factors to consider when selecting a robot for your operation.
Streamlining Logistics with Mobile Robots
The use of mobile robots in logistics has delivered substantial improvements in efficiency and process optimization. These robots take on repetitive, time-consuming tasks such as transporting inventory, stocking shelves, and assisting with order fulfillment. By doing so, they not only reduce manual workload but also allow employees to focus on more complex or value-added responsibilities.
One of the standout benefits is the consistent and uninterrupted workflow mobile robots offer. Their ability to operate around the clock minimizes delays and supports timely deliveries—an essential requirement in today’s just-in-time economy.
Strengthening Supply Chain Performance Through Robotics
Autonomous mobile robots bring a new level of precision and reliability to supply chain operations. Equipped with advanced sensors and navigation systems, these machines can safely maneuver through dynamic environments, adapting in real-time to obstacles and route changes.
By automating key processes such as material movement, product sorting, and inventory distribution, these robots help companies reduce errors and maintain a steady flow of goods throughout the supply chain. In doing so, they contribute to a higher quality of service, better product handling, and improved accuracy in order processing.
Core Advantages of Robotics in Supply Chain Automation
Implementing mobile robots in logistics environments yields several tangible benefits:
- Improved Inventory Accuracy: Robots can update stock levels in real-time, reducing discrepancies and ensuring accurate tracking.
- Continuous Workflow: Robots help maintain a seamless production cycle by autonomously managing replenishment tasks.
- Consistent Product Quality: Automation ensures steady performance, allowing companies to scale output without compromising quality.
- Operational Agility: Robots can quickly adapt to fluctuating demand, scaling activity up or down based on current needs.
Seamless Integration with Factory Systems
Incorporating mobile robots into existing automation infrastructure is increasingly achievable thanks to advances in software and interface compatibility. Robots can now communicate with warehouse management systems and control platforms using standardized protocols like OPC UA or MQTT. This enables coordinated task execution and real-time status updates.
Fleet management platforms also play a critical role, offering centralized control of multiple robots, task scheduling, and resource optimization. Additionally, the modular nature of many mobile robots allows them to be configured with specific tools or attachments, making them suitable for a variety of tasks in different environments.
Types of Mobile Robots Used in Logistics
Choosing the right robot depends on your operational requirements. Here are several common types:
- Wheeled Robots: Efficient and fast, these are ideal for moving goods in structured environments like distribution centers.
- Mobile Manipulators: These combine a mobile base with an integrated robotic arm, capable of both navigating and performing handling tasks.
- Autonomous Mobile Robots (AMRs): AMRs are fully independent, using onboard systems to move through complex settings without human intervention.
- Collaborative Mobile Robots: Designed to operate alongside humans, these robots assist in shared workspaces, safely handling tasks like material transport or order picking.
What to Consider When Choosing a Mobile Robot
To ensure a successful deployment, companies must evaluate several factors:
- Payload Requirements: The robot must support the weight and size of the items it’s expected to carry.
- Operating Conditions: Floor type, temperature, and space constraints can influence robot performance and durability.
- Safety and Navigation: Choose robots with reliable sensors and navigation systems to ensure safe and efficient movement.
- System Compatibility: Integration with existing automation and IT systems is essential for full functionality and seamless operations.
Looking Ahead: Robotics and the Future of Logistics
Mobile robots are playing a transformative role in modern logistics. By automating repetitive processes, they reduce costs, improve efficiency, and bring new levels of flexibility to operations. While the vision of a fully autonomous supply chain is still evolving, the integration of mobile robotics is accelerating this progress.
As companies focus more on resilience, speed, and sustainability, mobile robots will become central to building smarter, more agile supply networks. Their continued development and adoption signal a significant shift toward intelligent automation across the logistics industry.