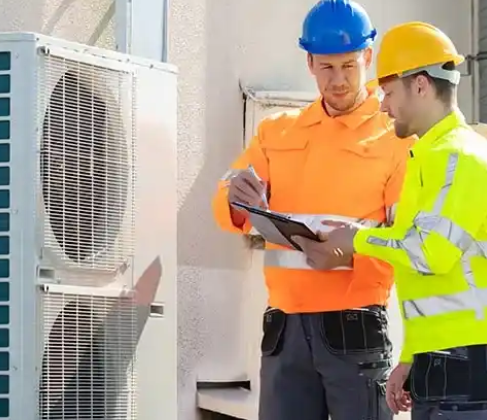
The integration of industrial robots into various sectors demands a strong focus on safety, both for operators and for the machines themselves. As robots become increasingly capable and widespread, safety protocols continue to evolve to address the emerging challenges posed by new technologies and applications.
This article explores the key safety standards and practices that ensure safe collaboration between humans and robots while maximizing efficiency in industrial settings. By adhering to these guidelines, manufacturers can foster a safer, more productive working environment.
What Are the Safety Standards for Industrial Robots?
Industrial robots, if not properly regulated, can pose significant risks, including unexpected movements, system failures, and electrical hazards. As robots become more integrated into complex operations, ensuring robust safety measures is critical.
To address these challenges, Robotnik follows strict safety standards to guarantee that their robots operate both safely and efficiently in diverse industrial environments. These measures include adhering to international regulations, using advanced safety systems like programmable logic controllers (PLCs) and LIDAR (Light Detection and Ranging) sensors, and conducting ongoing risk assessments to reduce hazards.
Key Safety Standards for Robotics
Several key international safety standards govern the use of robots in industrial applications, establishing minimum requirements to ensure safety:
- ISO 10218-1:2011: Specifies safety requirements for industrial robots.
- ISO 10218-2:2011: Focuses on the safety of robotic systems and their integration into existing operations.
- ISO 3691-4: Pertains to the safety of industrial mobile robots, such as Robotnik’s RB-KAIROS+.
- ISO/TS 15066: Covers the safety standards for collaborative robotic arms, ensuring safe interaction between robots and human operators.
These standards define crucial concepts like collaborative workspaces, risk categories, and safety functions, and they provide guidelines on risk analysis, protective measures, and operator training.
CE Marking: A Symbol of Compliance
The CE marking indicates that a product complies with the European Union’s health and safety regulations. The RB-KAIROS+ mobile manipulator robot is CE marked, ensuring that it meets all relevant safety standards and has passed the required conformity assessments. This certification reassures users that the robot is safe for operation in various industrial environments, aligning with European directives and guaranteeing that it meets all necessary legal requirements.
The Role of Safety PLCs in Robotics
The Safety Programmable Logic Controller (PLC) is a vital component of the RB-KAIROS+ robot, specifically designed to manage safety in industrial applications. Complying with international standards like IEC 61508 (SIL) and ISO 13849 (PLd or PLe), the Safety PLC monitors critical safety sensors such as optical barriers, laser scanners, and emergency stops. It ensures that the robot can operate collaboratively with humans, reacting swiftly to potential risks and maintaining a safe environment.
Key features of safety PLCs include:
- Continuous Monitoring: The PLC constantly checks for system failures and triggers automatic protection measures when necessary.
- Redundancy: Many safety PLCs have backup systems to ensure that the robot continues to function even if one component fails.
- Interoperability: The PLC easily integrates with other safety systems, enhancing the overall safety infrastructure.
The Importance of LIDAR in Robot Safety
LIDAR sensors are crucial for ensuring safety in dynamic environments. These sensors use laser technology to map the surroundings, detecting obstacles or people in real-time. For example, the RB-KAIROS+ robot uses LIDAR with PLd (Performance Level d) certification, which allows the robot to:
- Detect objects accurately at a significant distance.
- React in real-time to obstacles or potentially dangerous situations.
- Adapt to changing environments, ensuring that the robot can navigate safely in dynamic conditions.
Collaborative Robotics: Ensuring Safe Human-Robot Interaction
The growing use of collaborative robots (cobots) in industrial environments underscores the importance of adhering to safety standards. Collaborative robots work alongside human operators, requiring special attention to ensure safe interaction.
For cobots like the RB-KAIROS+, safety measures include:
- Force and Speed Limitation: Robots are programmed to limit their speed and force when interacting with humans to avoid injury.
- Safety Sensors: Work areas are monitored using sensors and security systems to prevent collisions and ensure safe operation.
- Risk Assessments: Detailed assessments identify potential hazards and implement strategies to mitigate these risks during robot deployment.
Conclusion: The Future of Safe Robotics
As industrial robotics become more advanced, it is essential for manufacturers and users to prioritize safety in robot design, deployment, and operation. Robots like the RB-KAIROS+ are built to comply with international safety standards such as CE marking, ISO certifications, and advanced safety systems like PLCs and LIDAR. These safety measures not only protect operators but also optimize production processes, enhancing efficiency and competitiveness in the market.
By adhering to these comprehensive safety guidelines, the robotics industry can continue to grow, ensuring a reliable and secure environment for both human workers and robotic systems.