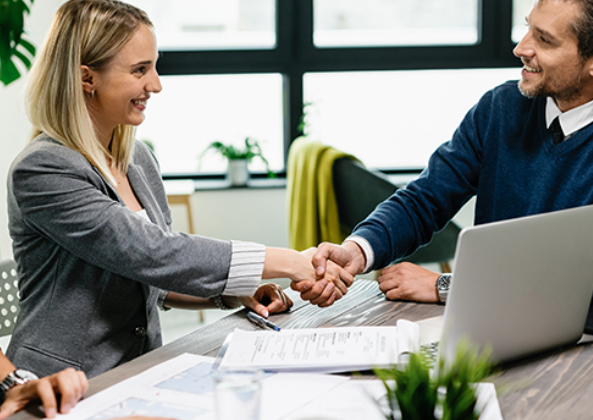
Supply chains are not all created equal. Various industries face different challenges, and their supply chain operations must be tailored accordingly. While the core principles of supply chain management remain the same, how they’re implemented can vary greatly depending on the nature of the products and the specific demands of the market. In this article, we’ll take a closer look at four distinct types of supply chains and the unique hurdles each one faces.
1. Building Products Supply Chain
The building products supply chain is among the most demanding when it comes to logistics. The primary challenge here lies in managing heavy, large, and often custom-manufactured components like concrete pipes, manholes, and structural elements, which can exceed 10 tons per piece. These items require specialized transport and handling, further complicating the logistics process.
Additionally, this sector is characterized by tight financial margins—usually 15-25% for standard items and even lower for custom pieces. Transportation costs are a significant part of the overall expense, often accounting for 20-30% of a product’s value. To maintain profitability, companies typically limit delivery distances to within 150-200 km.
Weather conditions also have a big impact, with delays in construction projects leading to a domino effect of disruptions. A single rain delay can halt a concrete pour, which then affects other scheduled deliveries, resulting in costly rescheduling.
In addition to these challenges, production schedules on building sites require precise coordination among different trades, which demands a high level of planning. Timely deliveries are crucial to avoid incurring significant costs from idle crews.
2. Grocery Retail Supply Chain
Grocery retail supply chains are notoriously complex, managing thousands of different products across various temperature zones. A typical supermarket network can carry anywhere between 20,000 and 40,000 SKUs. The volume of transactions in grocery logistics is staggering, with a large-format store processing over 40,000 customer transactions per week.
The key to success in grocery supply chains is on-shelf availability. Even a 1% improvement in shelf availability can result in a 0.25% increase in sales, so maintaining precise inventory levels is crucial. Stock-outs in this industry are especially problematic because they lead to lost sales and customers turning to competitors.
Temperature control adds another layer of difficulty. Products must be transported and stored across three main temperature streams: ambient, chilled, and frozen. This requires careful planning and coordination to ensure the integrity of the cold chain is maintained.
Additionally, grocery supply chains face unique challenges when distributing to urban areas. High-density cities with limited space and restricted delivery windows complicate logistics, requiring multiple deliveries to stores per day, each with different temperature requirements.
3. Healthcare Supply Chain
Healthcare supply chains operate under strict regulations and high stakes. Stockouts in healthcare can lead to disastrous outcomes, as shortages of critical supplies can delay surgeries or impact patient care. Hospitals often keep much larger inventories of essential items than typical businesses, maintaining 30-40 days of stock for key items to avoid shortages.
Temperature control is even more stringent in healthcare than in many other industries. Pharmaceuticals must be stored at precise temperatures, with some products needing storage as low as -80°C. This requires continuous monitoring, as even the smallest failure can result in the destruction of valuable stock.
The management of controlled substances adds further complexity, as hospitals must ensure these items are securely stored and carefully tracked. Every item is accounted for with serialized barcodes, and the loss of a single item can trigger a thorough investigation.
The recall process in healthcare is also demanding, requiring supply chain teams to act quickly to locate and quarantine affected products. This can involve checking supplies across multiple locations, which is time-consuming and labor-intensive.
4. Oil and Gas Supply Chain
The oil and gas supply chain is centered around maximizing equipment uptime. Any downtime in drilling operations can result in substantial financial losses—often as much as $200,000 to $400,000 per day. To prevent this, companies maintain large inventories of critical spare parts, sometimes worth millions of dollars.
Spare parts management is complex, with offshore platforms typically keeping between 15,000-20,000 SKUs on hand. Many of these parts are slow-moving, meaning they might not be used for years, but they are essential when needed. Inventory audits are a regular part of operations to ensure that everything is accounted for.
Transportation logistics in the oil and gas sector present their own challenges. When urgent parts are needed offshore, they can’t simply be shipped by standard methods. Many operations rely on dedicated helicopter services to deliver critical components quickly, which can cost tens of thousands of dollars per flight.
Maintenance planning is critical in this industry. Platforms schedule major maintenance shutdowns up to two years in advance, ensuring that all parts and contractors are coordinated. The cost of errors in these shutdowns can run into millions of dollars.
Conclusion
Supply chains vary greatly across different industries, with each one facing unique challenges. Whether dealing with heavy construction materials, perishable groceries, life-saving medical supplies, or high-cost oil and gas components, each sector requires a tailored approach to supply chain management. Understanding these nuances is crucial for businesses to develop effective strategies that address the specific needs of their operations.