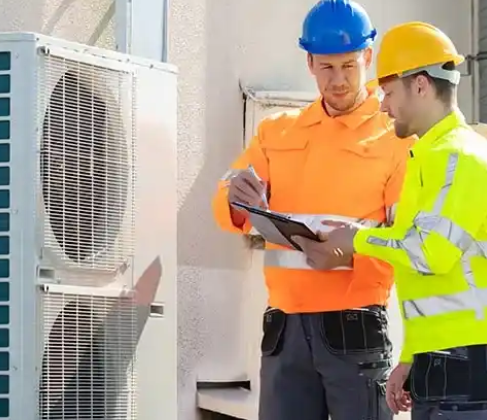
When designing an effective distribution center (DC), there are several key factors to consider, making it a complex task for many logistics professionals. The design needs to be both efficient and scalable to ensure smooth operations, whether you’re building a new facility or upgrading an existing one. Let’s explore some essential design principles and tips for optimizing warehouse layout and functionality.
Key Warehouse Layouts
I-Shaped Design
The I-shaped design features separate areas for receiving and dispatching, typically located at opposite ends of the warehouse. This flow-through layout is ideal for high-volume operations where distinct separation between receiving and shipping is required. However, this design demands more space for vehicle maneuvering than alternatives like the U- or L-shaped layouts.
U-Shaped Design
In a U-shaped design, receiving and dispatching areas are positioned adjacent to one another. This layout is commonly used because it optimizes land use by minimizing the hardstand area needed for vehicle movements. The U-shape provides an efficient ratio of building-to-land usage, making it a popular choice for warehouses that deal with moderate-volume operations.
L-Shaped Design
The L-shaped design is used when receiving is done on one side of the warehouse, and dispatch occurs on an adjacent side. This layout is often used for cross-docking operations or businesses that receive large shipments but dispatch smaller loads. It offers a good balance of space optimization and operational flow.
Racking Orientation
The orientation of racking systems in your warehouse should align with the level of automation and material handling techniques you plan to use. For automated systems, such as Automated Guided Vehicles (AGVs) or Automated Mobile Robots (AMRs), the rack orientation is less critical, as these systems are capable of navigating various layouts efficiently.
In manual operations, it’s more beneficial to align racking parallel to receiving docks, minimizing travel time for forklifts and other manual handling equipment. For mixed operations, where both automated and manual processes coexist, a zone-based layout can offer the best of both worlds, with automated sections running perpendicular to traditional manual zones.
Level of Mechanization
When determining the level of mechanization for your distribution center, consider the number of products (SKUs) and the volume of orders processed. In modern operations, picking often consumes a significant portion of resources, but with automation, this percentage has dropped. Technologies like goods-to-person systems and robotic picking have transformed picking operations, reducing labor costs and improving speed.
The right balance of mechanization depends on factors such as order volume, labor availability, and ROI on automation systems. Investing in mechanization may reduce long-term operational costs, but over-investing can strain your budget.
Dock and Loading Bay Design
Proper design of docks and loading bays is crucial for smooth operations. Consider the variety of vehicles visiting your facility, including large trailers, temperature-controlled units, and smaller delivery vehicles. A well-designed dock layout will ensure efficient vehicle flow, minimizing congestion and delays.
Warehouse Height Considerations
Warehouse height has evolved significantly over the past decade, with modern facilities reaching up to 30-40 meters in height. This change is driven by the adoption of automated systems like Automated Storage and Retrieval Systems (AS/RS) that allow for efficient use of vertical space. The rise in land costs in urban areas has also pushed developers to build taller, multi-story warehouses.
For new distribution centers, the recommended clear height ranges from:
- 15-18 meters for standard distribution,
- 20-25 meters for e-commerce fulfillment,
- 30-40 meters for fully automated facilities.
Practical Tips for Distribution Centre Design
Warehouse Aspect Ratio
The ideal warehouse shape is rectangular, with a length-to-width ratio of about 1.7:1. Avoid circular, triangular, or irregular shapes as these tend to be inefficient for logistics operations.
Space Allocation
For modern warehouses, the traditional 75/25 split between storage and receiving/dispatch space is outdated. Today’s facilities should allocate 35-40% of their floor space to receiving and dispatch operations to accommodate returns processing, last-mile staging, and automated sortation. The remaining space can be divided between storage, picking zones, and value-added services.
Vehicle Flow and Turning Space
When designing your loading docks, ensure there’s enough space for large vehicles to maneuver. For semi-trailers, allow 37 to 40 meters of space for turning and reversing. For B-doubles, 50 to 55 meters is ideal, though some designs may reduce this requirement by eliminating the need for reversing.
Space per Pallet
For conventional selective racking, allow approximately 1.2 square meters per pallet. In narrow aisle or double deep systems, this can increase to around 1.4 square meters.
Choosing the Right Distribution Centre Location
Selecting the ideal location for your distribution center is critical for efficient logistics. Here are a few tips to guide your decision:
- Proximity to Demand: Your distribution centers should be close to where your customers are located. High-density urban areas are typically the best choice for fast-moving consumer goods.
- Access to Transportation: Ensure the location is well-connected to major roads, highways, and ports to facilitate smooth inbound and outbound traffic.
- Weighing Transport Costs: While land and building costs are important, consider the impact of transport costs on your overall distribution expenses. Proximity to key infrastructure can significantly reduce long-term shipping costs.
- E-commerce Considerations: With the rise of online shopping, proximity to customer hubs is even more important. Same-day or next-day delivery has become a key competitive advantage, making efficient fulfillment and distribution critical.
Conclusion
Designing a distribution center requires thoughtful planning and attention to key factors such as layout, racking systems, mechanization, and location. By optimizing these elements, you can create a facility that improves efficiency, reduces costs, and scales with your business’s needs. Whether you’re focused on e-commerce, retail, or B2B operations, a well-designed DC will enable your company to stay competitive in today’s fast-paced logistics landscape.