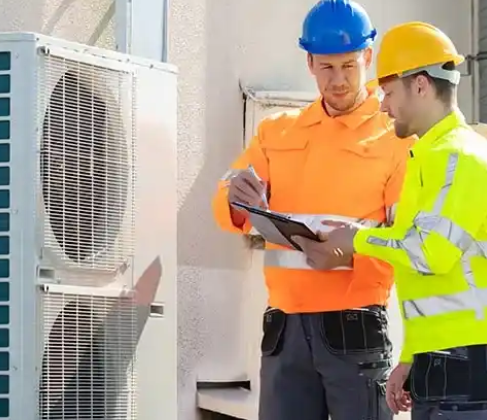
In today’s competitive industrial landscape, automation continues to play a critical role in streamlining production processes. Among the key technologies leading this transformation are manipulator robots—sophisticated machines designed to handle, move, and position objects with precision. Originally developed for high-risk environments, these robots have evolved far beyond their initial applications, now offering enhanced mobility and versatility across various sectors.
What Exactly Is a Manipulator Robot?
A manipulator robot is a robotic system built to perform tasks that involve handling physical objects. Traditionally, these systems consist of a stationary robotic arm equipped with a specialized tool (end effector) such as a gripper, vacuum suction, or screwdriver. These robots were initially deployed in hazardous conditions where human intervention posed significant risks, including radioactive zones or high-temperature environments.
Today, the concept has expanded to include mobile manipulators—robots that integrate a mechanical arm with a mobile platform. This combination allows them to navigate across industrial spaces while performing complex manipulation tasks, significantly broadening their capabilities.
Mobile Manipulators: Combining Movement and Dexterity
Mobile manipulator robots stand out for their ability to move autonomously while handling materials. They’re commonly used in logistics and manufacturing, where they transport goods or assemble components across different workstations. Equipped with an array of sensors like LiDAR, 3D cameras, and ultrasound, these machines can detect obstacles, plan efficient routes, and adjust to dynamic environments.
With advancements in machine learning and sensor integration, modern mobile manipulators are capable of mapping their surroundings in real time, optimizing their tasks based on learned behaviors, and improving both safety and accuracy in operation.
Core Capabilities of Manipulator Robots
Manipulator robots are engineered for high precision and adaptability. Their key strengths include:
- Versatile Handling: Able to manipulate items of varying shapes, sizes, and weights, these robots are suited for tasks ranging from product assembly to order fulfillment.
- Sensor-Driven Awareness: By leveraging cameras, force sensors, and proximity detection, manipulator robots can respond intelligently to changes in their environment.
- Operation in Harsh Conditions: These systems are ideal for roles in high-risk environments such as welding shops, painting stations, or areas with toxic exposure—situations that are unsafe for humans.
Enhancing Collaboration in Industrial Settings
Modern robotics increasingly focuses on collaboration. Manipulator robots can be integrated into workflows that involve close interaction with human workers or other robots.
- Human-Robot Collaboration: In shared workspaces, mobile manipulators assist operators by either taking over repetitive tasks or working alongside them to complete larger objectives.
- Robot-to-Robot Coordination: Multiple robotic units can collaborate to carry out complex workflows—such as inventory movement or synchronized assembly—by sharing data and responsibilities.
These collaborative features make robotic systems more adaptable and safer, particularly in manufacturing environments where flexibility is essential.
Industrial Automation and Collaborative Robotics
While robotics has progressed significantly, challenges remain—particularly in enhancing payload capacity, refining user interfaces, and ensuring safe interaction with humans. Some strategies to address these include:
- Load Optimization: Newer models like those using the UR20 arm are capable of lifting up to 20 kilograms, expanding the scope of what mobile manipulators can achieve.
- User-Friendly Controls: Touchscreens, voice commands, and intuitive software interfaces help bridge the gap between human users and complex robotic systems.
- Smart Sensing: Advanced machine vision and navigation sensors allow for responsive interaction and real-time obstacle avoidance.
- Safe Movement Planning: Algorithms must take human presence into account and adjust routes to avoid accidents, ensuring smooth operation in shared environments.
Practical Applications Across Industries
Mobile manipulation robots are versatile and can perform a variety of functions across different settings. Here are a few examples:
- Material Transport: Robots can move raw materials, parts, or finished goods across facilities, helping streamline internal logistics.
- Order Fulfillment: They can pick items from shelves and prepare them for shipping based on customer orders, improving warehouse efficiency.
- Quality Assurance: Equipped with vision systems, robots can perform detailed inspections to identify product flaws and verify assembly accuracy.
- Medical Logistics: In healthcare environments, robots help transport medication, deliver samples, and manage supply chains within hospitals.
Looking Ahead: Trends in Robotic Manipulation
Innovation continues to expand the capabilities of manipulator robots. From integrating more adaptable end effectors to improving machine intelligence, the possibilities are rapidly growing. These developments are fueling a broader adoption of collaborative mobile robots, especially as industries look to optimize flexibility, safety, and performance.
In conclusion, manipulator robots offer substantial benefits in terms of speed, accuracy, and safety. Their expanding roles in sectors such as automotive, electronics, healthcare, and logistics underscore their importance in the transition toward Industry 4.0. As advancements in robotics continue to evolve, manipulator systems are set to play an even more pivotal role in building agile, intelligent, and safer workplaces across the industrial spectrum.