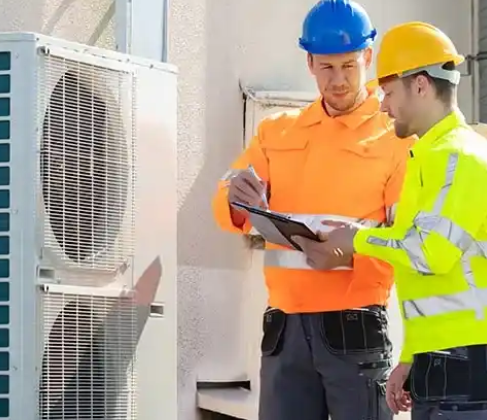
Material handling is a vital aspect of the supply chain, encompassing everything from the movement and storage of materials to their protection and final disposal. It plays a critical role in the efficiency of modern logistics, particularly in the manufacturing and distribution sectors.
In warehouses, the equipment used for material handling (MHE) ranges from basic tools like pallet jacks to advanced automated systems. The choice of material handling equipment significantly influences labor costs, throughput rates, and storage capacity.
Effective material handling can account for up to 25% of a facility’s operational costs. Optimizing these systems can lead to a dramatic improvement in productivity. Some businesses have managed to boost their throughput by up to 40% simply by refining their material handling processes and equipment choices.
Key Elements of Material Handling
Storage and Handling Systems
These are the racks, shelving, and containers used to store materials. A well-designed storage system maximizes space and accessibility. Facilities that utilize vertical storage solutions, for example, can increase their storage capacity by up to 40%.
Transport Equipment
This includes forklifts, conveyors, and Automated Guided Vehicles (AGVs) that help move materials within a facility. Choosing the right equipment depends on the layout of the facility and the volume of materials being handled.
Picking Systems
Picking refers to the process of selecting items from storage for order fulfillment. From simple manual picking to more advanced systems like voice-directed or pick-to-light systems, the goal is to improve both speed and accuracy. Modern systems can achieve error rates of less than one mistake per thousand picks.
Loading and Unloading Equipment
This category includes dock levelers, pallet inverters, and truck restraints, all of which are essential for transferring materials safely and efficiently between vehicles and warehouses.
Why Material Handling Matters
Material handling is not just about moving things from one place to another; it directly impacts the efficiency and costs of warehouse operations. In fact, labor costs typically make up the largest portion of a warehouse’s operational budget. A poorly designed material handling system can lead to:
- Slower order fulfillment times
- Increased labor costs and decreased productivity
- Poor use of available space
- Higher risks of inventory damage and loss
- Increased operational costs
Improper material handling can also cause significant bottlenecks in the workflow, preventing businesses from meeting their production and delivery targets.
The Cost of Poor Material Handling Decisions
Unfortunately, many companies treat material handling as an afterthought, failing to recognize its importance in the broader strategic picture. This leads to inefficient operations, higher labor costs, and the risk of missing deadlines or failing to meet customer expectations.
Making smart material handling choices and investing in the right equipment can transform operational performance. Efficient material handling not only reduces costs but also improves safety, space utilization, and overall productivity.