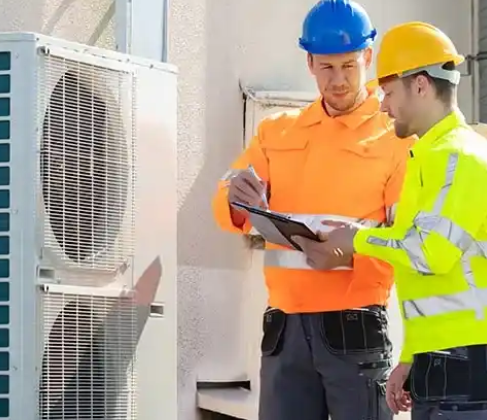
Lead time plays a crucial role in the smooth functioning of a supply chain. It refers to the total time required for a product or material to pass through the supply chain, from placing an order to receiving the product. Efficient lead time management ensures cost control, streamlined operations, and improved customer satisfaction.
The process of lead time management involves various stages such as order processing, sourcing raw materials, manufacturing, shipping, and final delivery. By understanding these stages, businesses can pinpoint where delays may occur and work towards minimizing them. Improving lead time not only enhances operational efficiency but also positively impacts customer service, inventory control, and overall supply chain performance.
What Exactly is Lead Time?
Lead time in the supply chain is the time it takes to fulfill an order from when it’s placed to when it’s delivered to the customer. This includes several key steps: order processing, sourcing materials, manufacturing, transportation, and delivery. Each of these activities contributes to the total lead time, and understanding how each one operates is vital for managing and reducing delays.
Why is lead time so important? Simply put, time is money. The longer the lead time, the more resources are used to move a product from one stage to another. In addition to the financial impact, longer lead times can negatively affect customer satisfaction, which can ultimately hurt a company’s reputation and competitive edge.
Reducing lead times not only saves money but also helps to maintain good customer relationships by meeting delivery expectations. Therefore, businesses need to focus on minimizing bottlenecks, inefficiencies, and waste that extend lead time, as this will have direct and indirect financial implications.
The Importance of Measuring Lead Time
Even if your company has successfully optimized its lead time, it’s still essential to measure it regularly. Tracking lead time provides valuable insights into service performance, inventory management, and overall coordination across the supply chain.
Here’s how accurate lead time measurement can benefit your business:
- Customer Satisfaction: By understanding and communicating accurate lead times, you can set realistic expectations for customers, ensuring timely deliveries and fostering trust.
- Inventory Management: Knowing your lead times helps you maintain optimal inventory levels, ensuring that you have the right stock at the right time without overstocking or running out of items.
- Supply Chain Coordination: Having a clear understanding of lead times across all areas of the supply chain helps different teams synchronize efforts, reducing delays and increasing overall efficiency.
Different Types of Lead Time
Lead time is not a one-size-fits-all concept. It can vary across different stages and processes within the supply chain. Here are some types of lead time:
- Upstream Lead Time: The time it takes for raw materials, components, or finished goods to reach your company’s production or storage facilities.
- Downstream Lead Time: The time required to move finished products from your company to your customers.
- Total Lead Time: The combined time of upstream and downstream lead times.
- Production Lead Time: The time spent manufacturing a product, from sourcing raw materials to completing the final product.
- Transportation Lead Time: The time it takes to transport goods from their source to their destination.
- Inventory Lead Time: The time it takes for stock to be ordered and entered into inventory records.
- Order Processing Lead Time: The time from when an order is placed to when it’s ready to be shipped.
- Customer Lead Time: The total time from order placement to delivery, including all the stages of order processing and shipping.
- Supplier Lead Time: The time it takes for suppliers to fulfill your orders for products or materials.
- Material Lead Time: The time from placing an order for materials to their arrival at your production facility.
Key Factors Impacting Lead Time
A wide range of factors can influence lead times in the supply chain. Some factors are within your control, while others are external and can’t be avoided. Here are some of the most important internal and external factors:
Internal Factors:
- Production Capacity and Efficiency: The availability of resources, labor, and equipment at your manufacturing facilities plays a critical role in determining production lead times. Efficient operations and proper maintenance help keep lead times low.
- Inventory Management Practices: Effective inventory management ensures that stock levels are optimized, reducing the chances of delays caused by stockouts or excess inventory.
- Transportation Methods: Efficient transportation planning and route optimization are crucial for minimizing delays in shipping. The mode of transportation—whether by air, sea, or land—has a significant impact on lead times.
External Factors:
- Geographical Distance: The distance between suppliers and customers plays a key role in transportation times. Longer distances naturally lead to longer lead times.
- Demand Variability: Unexpected fluctuations in demand can disrupt production and shipping schedules, leading to longer lead times. Companies must be prepared to adjust their operations based on demand changes.
- Supplier Performance: Reliable suppliers are essential for maintaining consistent lead times. If suppliers fail to meet deadlines, it directly affects your ability to meet customer expectations.
- Supply Chain Disruptions: Natural disasters, political instability, or other unexpected events can disrupt the flow of goods, causing delays in lead time.
- Regulatory and Customs Issues: Changes in customs regulations or the need for compliance with international shipping laws can add time to the supply chain process, especially for global shipments.
- Product Complexity: The more complex a product is, the more time it will take to manufacture, source materials for, and ship. Complex products are often more prone to delays, especially when external factors like transportation issues or supplier problems arise.
Effective Lead Time Management
Managing lead time can be challenging, but it’s a key factor in maintaining an efficient supply chain. While it’s tempting to focus solely on reducing lead time, it’s more important to optimize it. Reducing lead time too aggressively without considering external factors can actually make the supply chain more fragile.
The most effective lead time management strategy involves setting realistic expectations with your customers and continuously working to meet or exceed them. Communication is crucial—keeping customers informed about lead times ensures that they know when to expect their orders and helps maintain trust.
Ultimately, managing lead time is about finding the right balance between efficiency and reliability. When you manage lead time well, you can improve customer satisfaction, reduce costs, and build a more resilient supply chain.